The countdown is on. BMW plans to launch its New Class lineup at the end of this year. So while the electric iX3 is scheduled to roll off at the newly built plant in Debrecen, Hungary, production of the sedan is planned to start next year at BMW HQ in Munich. Accordingly, prep work is proceeding, and those in the thick of it have to ensure ongoing production continues while tomorrow’s can start smoothly. To achieve this level of seamlessness, many new elements of the BMW iFactory production concept will be implemented.
As the use of virtualisation, AI, and data science increased in 2020, BMW devised the iFactory, a breakthrough concept that networks every aspect of automotive production with 3D scanning of all vehicles and engine plants. Now, BMW aims to achieve new levels of efficiency by focusing on comprehensive digitalization.
The strategy is upheld by three central and closely linked pillars. One is data science since the basis of every decision rests on precise and comprehensive data. BMW, after all, places great emphasis on collecting and linking data from various sources in order to obtain a holistic picture of the production processes.
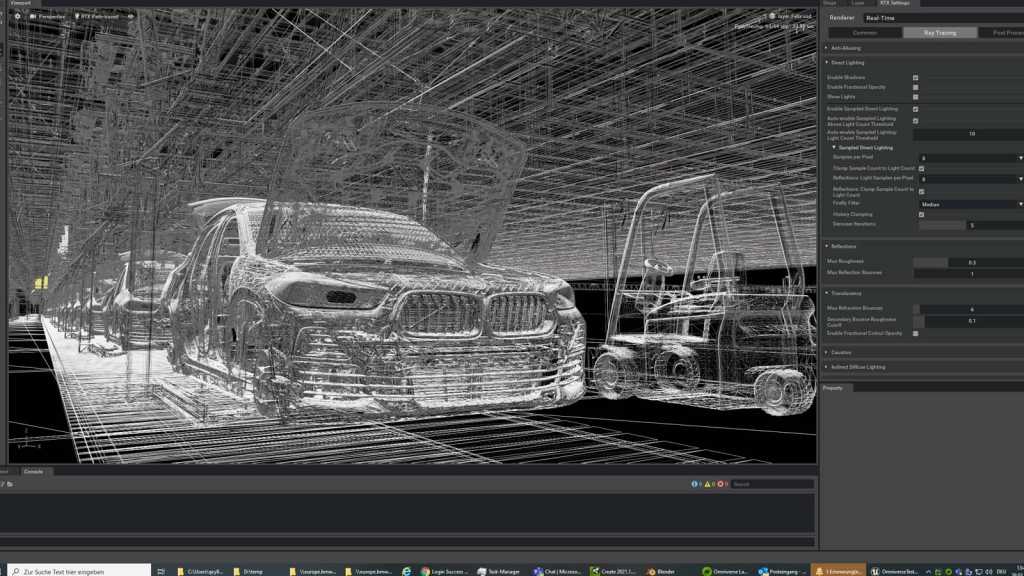
BMW Group
Then there’s AI, which is used to analyze processes and recognize patterns. Although AI is already used in many production processes, especially in quality control, BMW sees great potential for future applications as the technology evolves.
And by using digital twins of factories and processes, BMW plans, simulates, and optimizes processes using virtualization, the third pillar, before physical changes are made. At the heart of this transformation is the virtual factory, a digital twin of real or future production environments, which fundamentally changes the way BMW plans, optimizes, and operates its plants.
Time is of the essence
The vision is to optimize and control production in real time. To this end, BMW plans to further develop the virtual factory by combining the actual data from the plants with planning data to enable a holistic view of production. And in addition to planning data, meta-information about objects is also linked, such as energy consumption, weight, and costs.
Jürgen Wittmann, head of innovation, virtual factory, and virtual commissioning in BMW’s production department, is currently planning the New Class setup in Munich with the digital twin. The advantages, he says, are obvious. “I can meet with the necessary colleagues at any time in collaboration sessions and discuss topics,” he says. “These can also be external partners, planners, maintenance engineers, or architects. And thanks to the digital twin, we know exactly the current situation and can immediately see the impact of changes.”
BMW Group
But until that point, the current situation had to be documented. So with the support of Munich-based tech startup NavVis, BMW scanned all 12 vehicle plants with 3D scanners, generating high-res, panoramic images and precise point clouds. So these form the digital footprint of BMW’s plants and serve as the basis for virtual models of the factories. And because 3D scans are very time-consuming, BMW is automating the scanning process by using drones or integrating scanning technology into logistics vehicles.
In clear view
The data obtained this way is being used for the first time via the BMW FactoryViewer web application, which is actively used by about 3,500 employees every month. Among other things, it enables indoor street views, allowing employees to virtually move through the factories, and users can orient themselves using a mini-map, similar to Google Maps.
BMW Group
Plus, to quickly access specific areas affected by renovations, employees can set points of interest within the viewer and calculate measurements of areas and distances, which is particularly helpful for planning tasks.
Another option is to compare different plants within BMW FactoryViewer to identify best practices. There’s a crop and download function, for example, which is also useful to extract relevant areas from the point clouds and share them with external partners.
A consolidation of data
While virtual models of the plants are incorporated into the iFactory, with virtual simulation, optimization, and planning, that’s only half the battle. It’s also important to build in data from other disciplines such as architecture, plant engineering, and logistics. So data from different planning environments must be consolidated to create a unified and comprehensive planning process. To achieve this, BMW uses Nvidia’s Omniverse platform, which enables the integration of planning data from various sources and visualization in a unified 3D environment. The Universal Scene Description (USD) format, from the filming industry, plays a central role as it allows for the import and processing of different file formats without any loss of information.
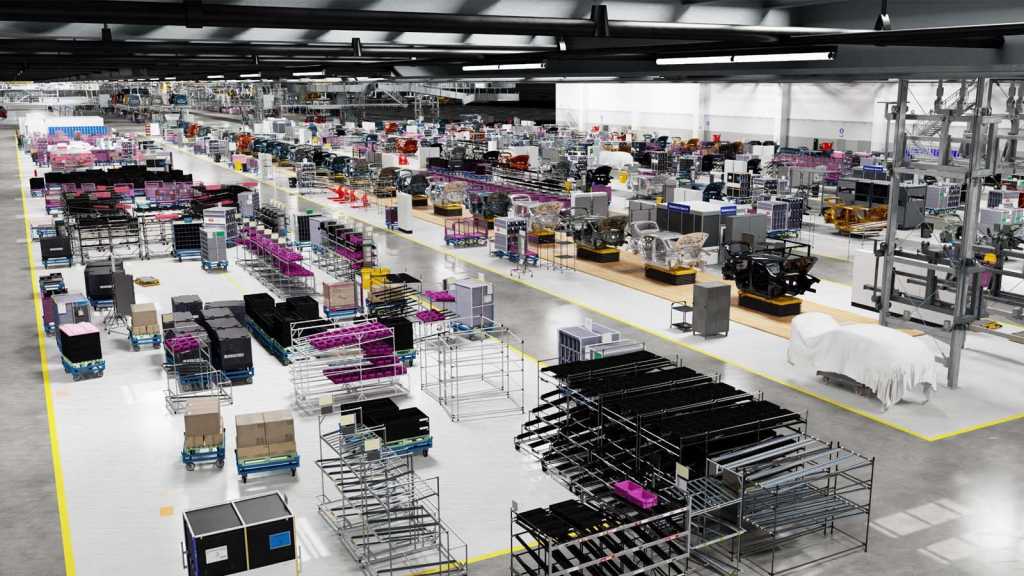
BMW Group
“USD is a format into which we can translate all common 3D information and data from the architect,” says Matthias Mayr, virtual factory specialist at BMW. “I can see exactly where systems are located and how much space they require without conflicting with disruptive factors. And this is true even though the systems were created with another digital tool.”
Parts of the whole
Ultimately, BMW Group production planners use Omniverse to consolidate planning data from various sources into a holistic 3D environment. Employees access the data via a web-based application, which allows planners to freely navigate the virtual environment, create cross-section through models, and examine different planning options. Furthermore, they can set waypoints to highlight specific planning points during discussions.
But the potential of the BMW’s Virtual Factory extends even further. Collision checks can be performed in the virtual environment to detect planning errors early, and motion sequences can be simulated to prevent collisions caused by moving parts, such as robots from the outset.
However, the simulation isn’t limited to the movement sequences of robots. Personnel and time resources can also be simulated and optimized in the virtual environment. This allows target times for specific activities to be defined, which can then be applied in the simulation to optimize workflows. Aspects of human ergonomics are also taken into account.
Maximizing economies of scale, and time
The digital twin in the metaverse is also expected to shorten planning times. For example, simulations of car bodies through the paint line can be completed within one to two weeks, whereas previously this took up to 12 weeks.
As impressive as these results are already, it’s only a first step for BMW on the path to the ideal iFactory. The BMW Group’s Virtual Factory is continuously being developed, and the next step will be to integrate operational data to optimize and control production in real time. This makes the virtual factory with the digital twin not only a planning tool, but a platform for innovation and collaboration, which demonstrates how digitalization can shape the future of production.
Read More from This Article: The digital mechanics that drive BMW’s latest rollout
Source: News